
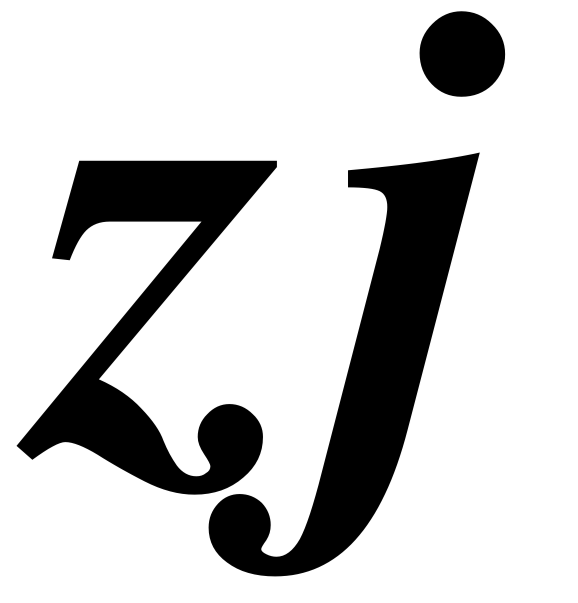
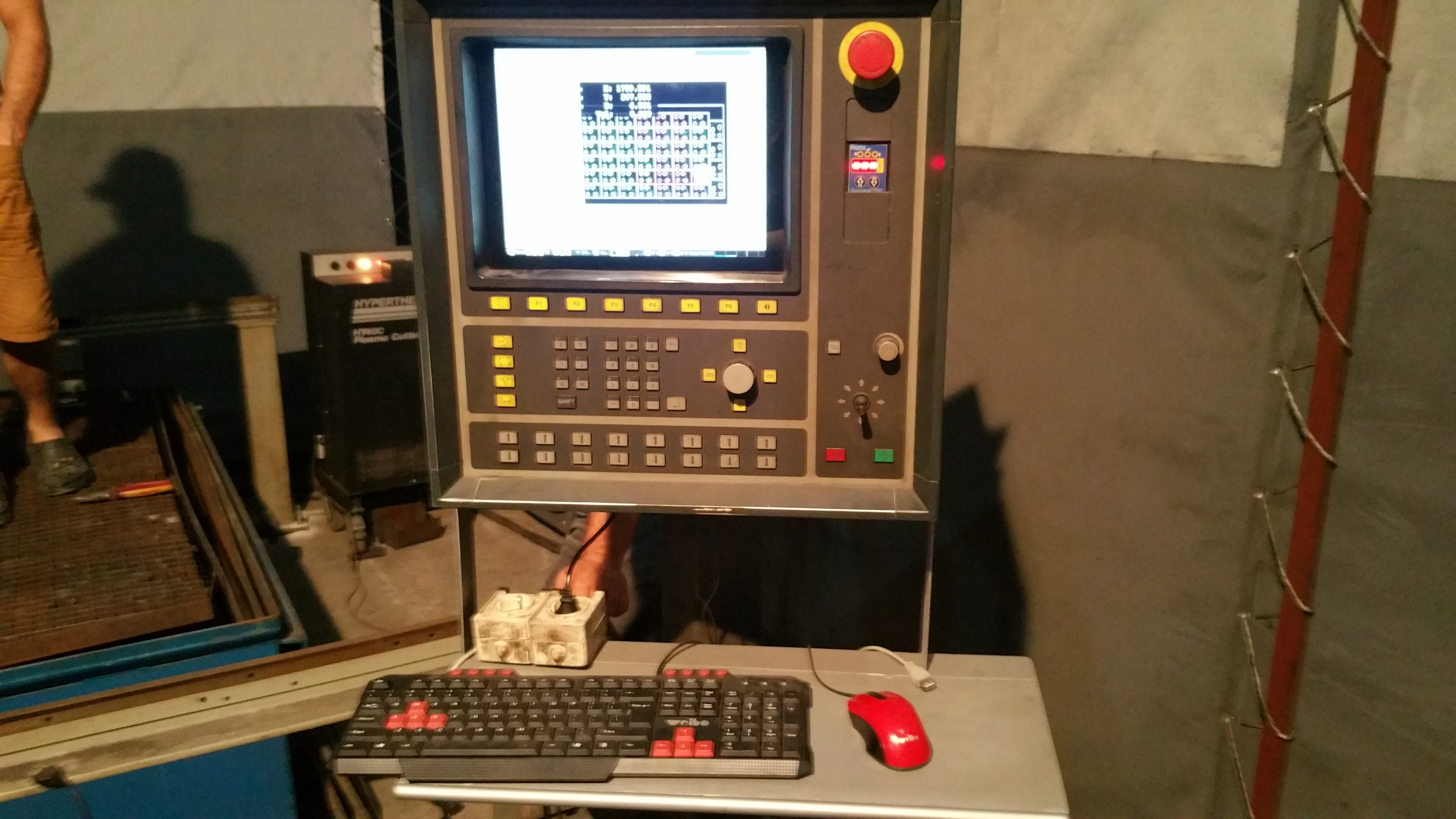
Energy-savings features can interfere w/ sending data to the Arduino. USB port has gone into low-power mode.Previous operation was quit from the Communication / Control program w/o disconnecting.Auto cycle start has been turned off - Note that turning off auto cycle start requires that one begin the machine manually.However, the active state goes to "Queue" and never returns to "Idle. The console window will show the command being sent and a confirmation of "ok". Repeat for back and forth movement, and up and down too, if that's also causing problems. Does the entire gantry move with respect to the stationary rails? You have loose V-wheels or eccentric spacers. Does the pulley turn too? You have a loose pulley set screw. Does the belt move but the pulley doesn't turn? You have a loose belt. Can you move it? If you can, watch carefully to see what moves with it. Try to wiggle the spindle left and right by hand. Turn the machine on, so that the motors energize, but don't tell it to move. Remain nearby until the cut is finished.Click the Carve button in the very top right to start cutting the design.This is your zero position that corresponds to the bottom left corner of your Easel workspace. Manually move the router head to the front left corner, and manually rotate the Z-screw until the tip of the router bit is touching the top of your workpiece.Arrange your design in the workspace and set the final depth of cut that you'd like.In the top right of the Easel interface, choose your material type (this determines safe feed rates) and material dimensions.Draw a simple design directly in Easel, or design something in Inkscape, save as an SVG and import into Easel.Login to Easel using the credentials found on the CNC router.
INKSCAPE GCODE LINUXCNC SOFTWARE
The Shapeoko can also be controlled with the workflow described above, but it also comes with a software package called Easel, which is meant to simplify the process. The benefit to this approach is that everything is done in a single program, and that the program is significantly more powerful and capable of handling 3D designs. Confirm that tool won’t collide with hold-downs by manually jogging machine around the pathĪnother method of using the CNC router is to use a program like FreeCAD to generate your 2D or 3D model, then also doing the CAM within FreeCAD.Move tool to origin and set the x, y, and z coordinates to zero by click Touch Off in LinuxCNC or by pressing Select + Direction Pad.Home machine by clicking Home All in LinuxCNC or by pressing Start + Select at the same time.Turn on CNC router by rotating E-stop button clockwise.Clamp down workpiece (Always use a spoil board!).Transfer gcode file to cncrouter computer using USB stick or /vsfs01/share directory.Create gcode: File -> Run Post Processor.Visualize the job with Mode -> Simulation.Set feeds and speeds (flip to other side for help).Create operations that assign tools to layers.Set job options (Options -> Job Options).Check machine options (Options -> Machine).Import drawing into SheetCAM (svg or dxf).Below is the general outline of this approach. If carving a 2D design like a sign, this is the quickest and simplest method. One method of getting from idea to CNC routed part is to create your CAD design in Inkscape, then use SheetCAM to generate the tool paths. The first is the most simple, the second more challenging but more powerful.
INKSCAPE GCODE LINUXCNC HOW TO
There are many ways to complete this workflow, but included in this section are descriptions of how to make a successful cut with two different sets of software.

The Phoenix and AXYZ CNC routers can both be controlled using their respective gamepad controllers. PROCEDURE General Controls and Configuration
